Zinc alloy die-casting electroplating processing technology is divided into two types, namely water electroplating process, and vacuum plating. The processing technology of water electroplating process is suitable for zinc alloy die-casting products; it is mainly to put the products that need electroplating process into the organic chemical electroplating process solution. electroplating process.
Vacuum pump plasma spraying, also known as vacuum electroplating; is suitable for zinc alloy die-casting products. At the same time, because of the disordered production process, the natural environment, and the high regulations on machinery and equipment, the price is more expensive than the water electroplating process.
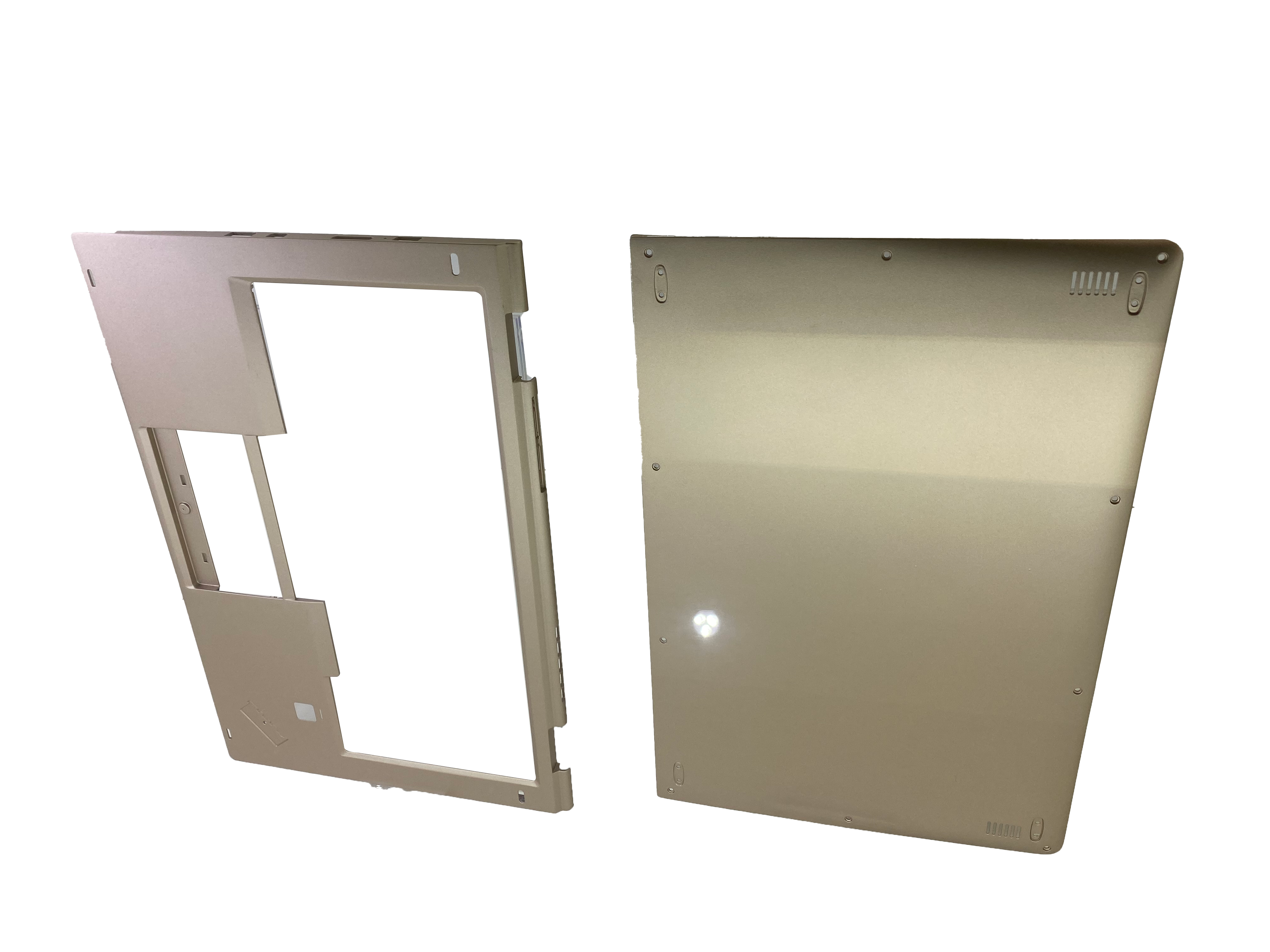
Many people do not know the difference between the two.
So what are the advantages and disadvantages of vacuum plating and water electroplating?
- Surface treatment: Generally, before the coating of the surface layer, the preparatory treatment such as degreasing and ash removal of the plate (plated part) is carried out to ensure the neatness and dullness of the plating part, and to avoid black spots and poor adhesion of the bottom coating layer. shortcoming. For special materials, such as PE (high pressure polyethylene) materials, etc., it is also solved to develop modified materials to achieve the estimated effect of the coating on the surface.
- Primer coating: During the construction of the primer coating project, spray painting or dip coating can be used. The details should be determined according to the specific conditions such as the size, appearance, structure of the plated parts, the customer's machinery and equipment, and the customer's quality regulations. By spray painting, SZ-97T surface coating oil can be used; by dip coating, SZ-97, SZ-97+1 and other oils can be used, and the details should be determined according to the material of the coating. Visit the integrated business scale of each commodity in the commodity presentation.
- Air-drying of the base coat: The coating oil series products on the surface are all self-drying paints, and the purpose of air-drying is to develop the output power of production. The general air-drying temperature is 60-70 ℃, and the time is about 2 hours. The stipulation for an air-drying finish is that the paint layer is thoroughly dull.
- Surface coating: When coating the surface, it should be ensured that after the vacuum value of the coating machine reaches the specified value, the filament should be heated again, and the heating time should be strictly controlled. At the same time, the number of metal materials (such as aluminum wire and cable) used for coating on the surface should be well controlled. Too little will cause walls or materials that cannot be hidden by the ceramic film. Too much will continue to endanger the life of the filament in addition to waste. and surface coating quality.
- Top coat: The general purpose of top coat has the following two levels:
- Develop the wear resistance, corrosion resistance and wear resistance of the plated parts;
- Show will be used for water staining.
- If the plated parts do not need to be colored, depending on the customer's requirements, 911, 911-1 matt oil, 889 full transparent oil, 910 matt oil and other surface oils can be used for spraying.
- Air-drying of the top coat: Generally, the top coat is thinner than the base coat, so the air-drying temperature is lower, about 50-60 degrees. The baking time can be flexibly controlled according to the customer's practical activity regulations. After all, it is necessary to ensure that the top coat is completely dry and boring.
- Water-staining dyeing: If the plated parts require water-staining dyeing, the plated parts that have already been dried can be put into the dyeing agent tank, stained with the desired color, and then eroded and dried. Pay attention to the operation of the dyeing agent. The temperature of the water, generally around 60-80 degrees, should control the time when the spring water is dyed. The disadvantage of water stain dyeing is that it is easy to fade, so the cost is lower.
Conclusion
For more information about die casting car parts,die casting process types,die casting mold cooling system, we are glad to answer for you.